Executive summary
The described processes within this paper should provide some insight into the complexity of the testing required to determine a protective coating’s ability to prevent or delay the effects of corrosion under insulation.
Some key points from within the paper:
- Select a test method, which allows you to determine the coatings resistance to heat / temperature, not just using the operating temperature as a guide but other likely conditions that the coating will encounter (upsets, thermal cycling etc.)
- Once this has been determined, identify a suitable test for corrosion under insulation and use this to determine the coating’s resistance. Consider the effects that any prior thermal exposure may have on the coating’s behaviour
- Where a coating has been selected for a dual use including atmospheric exposure, ensure that this has also been thoroughly evaluated, don’t simply rely on the corrosion under insulation test results
- Use protective coatings carefully as part of an overall CUI methodology, which includes optimal design, best installation practises and current inspection and detection techniques to prevent corrosion under insulation really hurting you
Introduction
Choosing the optimal coating for protection against corrosion under insulation (CUI) is a complex affair. This paper describes a number of tests that a coating should undergo in order to prove suitable for the specific function it is to fulfil.
CUI can lead to significantly lost revenue from downtime, maintenance and replacement of corroded parts. The wrong coating for the equipment can also prolong the entire project.
Both through tests and in actual projects, a fast and effective solution has proven to be Versiline CUI 56990. This coating reduces the overall lifecycle costs and ensures benefit from longer uptime.
It is resistant to temperatures from cryogenic (-196℃) up to 650℃, while at the same time, it is also resistant to thermal shock and cycling in dry or dry/wet service conditions.
This paper explains the necessary actions before choosing a coating that can protect the assets of any equipment operator in the process industry and thereby help support their business.
1. What to be aware of before choosing the right CUI coating
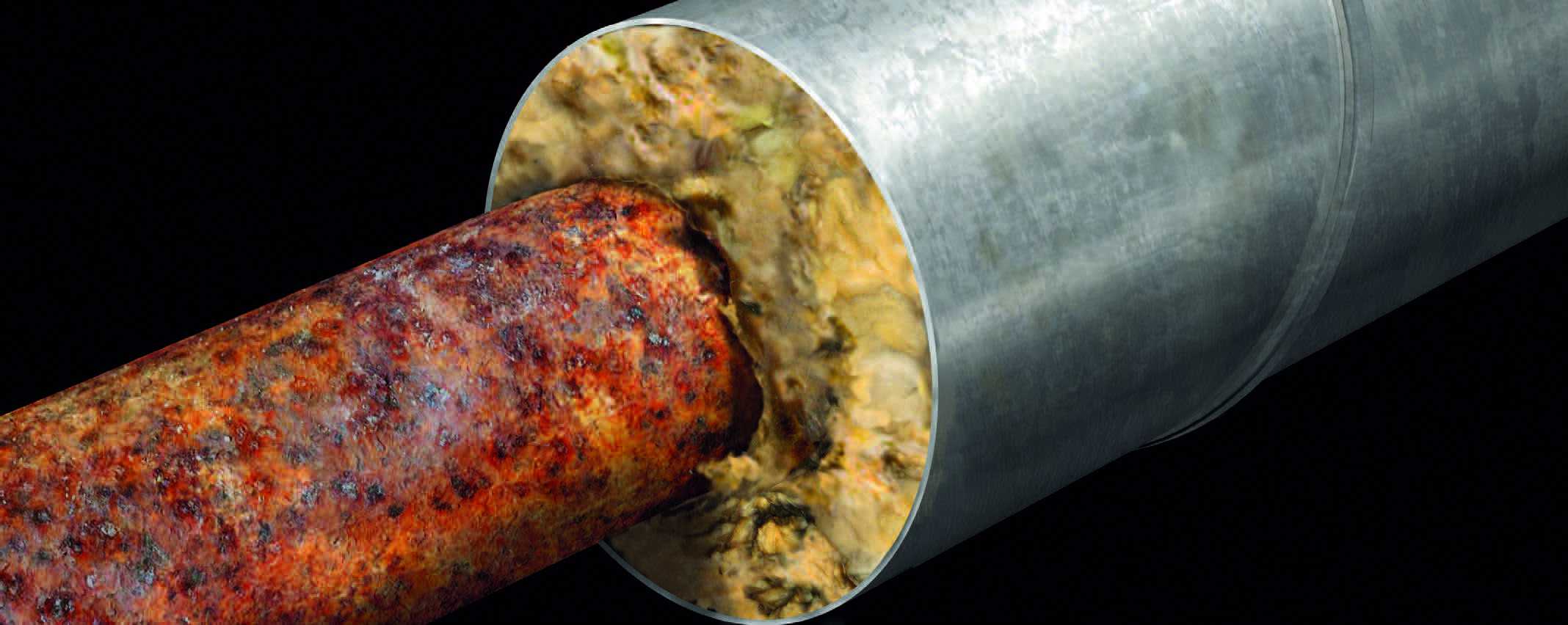
Many operators in the protective coatings business have seen the horror pictures of corrosion under insulation and appreciate that coatings can play a very important part in prevention of this problem. This has been known for many years and it makes sense that a number of those horror pictures were probably once newly coated pipes.
But what makes a coating system not provide the level of resistance expected in an insulated environment? And how can you make sure that you choose the right coating for a specific purpose?
In order to choose the right coating for the right material, it is necessary to look at which test protocols can be used to predict a coating material’s behaviour when placed in a CUI environment.
This paper provides an indication of some of the issues that make it important to ensure the correct specification of coating materials for CUI environments. It also presents how knowledge about the candidate coatings behaviour towards heat will help assist in correct material selection.
Furthermore, different coating tests will be discussed with the purpose of defining which methods can be used to simulate CUI conditions in the laboratory, and how to evaluate a coating material’s performance under related conditions.
A closer look at which tests can be used shows that it can be appropriate to look beyond test methods related to corrosion under insulation when considering protective coatings for insulated pipework and process equipment.
One of the major challenges that equipment operators in the process industries are facing today is CUI – and it can lead to significant lost revenue from downtime, maintenance and replacement of corroded material.
As this paper also presents, Versiline CUI 56990 may very well be the right choice of coating in an environment where corrosion under insulation can occur. Versiline has proven to provide long-term protection and its combination of heat resistant binder and barrier pigments make it highly effective against corrosion under insulation, even under cyclic conditions.
2. Challenges when finding the right CUI coating
When a coating for corrosion under insulation is found unsatisfactory, many factors play a role: Did the coating disappoint due to poor application? Was the product incorrectly specified? Or, more rarely, was the product defective itself? Above all, it is crucial is to determine if a coating is suitable or not for an environment where corrosion under insulation can occur, and so avoid specifying an unsuitable material.
Whilst of course the ability to prevent corrosion under insulation is of paramount importance, often when considering protective coatings to be used under insulation, particularly at the new construction stage, designers must consider them in the context of a wider painting specification.
In recent years, much focus has been placed on the ability of protective coatings to be used across a wider variety of temperature ranges, including cryogenic in both insulated and uninsulated service. The benefits of such systems can be significant and include:
- simplified coating specifications for pipework and process equipment
- reduced number of coating systems to approve for construction
- eliminating the need for separation of bulk items, such as piping and valves prior to painting
- simplified paint inventories for applicators
- streamlined coating and inspection procedures
While there is a tendency to assume that corrosion under insulation conditions are the most aggressive, this is not always the case. It depends on the generic type of the coating. Therefore, it is essential to also consider accelerated atmospheric corrosion when selecting coatings for a dual role.
Thermal conditions play a role in coating specifications
CUI is widely described as occurring in the temperature range of 50 -175° C. However, in the case of environments with high relative humidity – the so-called ‘sweating’ pipe syndrome – corrosion beneath insulation can occur below this temperature.
Of course, in the case of a modern paint specification, this temperature range is only one of many, generally resulting in specification of a variety of different paint systems. It is also fair to say that when specifying coating systems for new construction projects, protecting against CUI is simply one of many coating uses to be considered, albeit an important one.
Regarding the issue of temperature itself; a discrepancy in categorising the coatings by temperature range causes challenges. Whether the coating is defined by being able to withstand a minimum temperature, maximum temperature, maximum constant operating temperature, peak excursion temperature is of utmost importance. But many different terms are used and this may affect the product recommendations and choices significantly. An example of this is pipework coated with an Epoxy Novolac coating. Routinely operating at a “temperature” of 160°C beneath insulation, this temperature is not expected to pose any issues for this material. However, subject it to regular steaming out or process cycles to a peak operating temperature above 200°C, and it would not be unreasonable to expect to see degradation of the coating over a period of time, ultimately manifesting itself as coating failure. In the absence of a protective coating, CUI can then start to work its destructive cycle.
Also, how often do the process information and engineering drawings calculate the temperature? The reality between process temperatures and skin temperatures can be significant. This may take the pipe external temperature very clearly in to the range at which CUI occurs.
Here, it is also essential to be aware that the same coating does not necessarily work equally well at high and low temperatures. Many protective coatings undergo a transformation when exposed to heat. In some cases, this is necessary, such as in the case of some silicone resins where heat is needed in order to remove the organic binder and leave behind the hard heat resistant silicon matrix. They will definitely show different performance characteristics depending on the thermal conditions they have previously been exposed to.
So, when finding the right coating for the specific purpose, it is advised to look to different test methods depending on the thermal and functional challenges the coating has to be able to withstand.
Relevant coating tests
In order to better categorise coating materials for high heat and CUI type environments, the types of testing that could be considered can be divided into three main types:
- a) Those that we can use to characterise the material and its behaviour under thermal conditions.
- b) Tests that indicate the performance of the coating material when exposed to a real or simulated CUI environment.
- c) Tests that could reasonably be needed to determine a coating’s suitability for multiple uses, for example, if a coating for both insulated and uninsulated environments is demanded, what other proof of performance should then be considered in addition to 2) above.
In the following, the three different types are described respectively highlighted.
a) Coating characterisation tests
Many of the standard coating terms regularly seen on product data sheets can be used as a guide to what the material looks and feels like. Generic type, volume solids, VOC level, density are to name but a few. But how can a coating’s ability to resist temperature be measured?
ASTM D 2485 is used to determine a coating’s resistance to heat. This test exposes coated panels to a variety of different temperatures where they are left for a period of time. They are then allowed to cool off (either by air or water immersion), and inspected visually for any signs of blistering, cracking, flaking and delamination from the metal surface.
Following this, panels are exposed to a corrosive environment via accelerated corrosion testing for a limited time, or a real life atmospheric corrosion test. The purpose is here to identify any areas where heating of the coating has caused cracking, which may have penetrated to the substrate and subsequently be a site for corrosion. In this case, microcracks and CUI are very similar – what you cannot see can definitely hurt you.
Microscope evaluation of fibre reinforced thick film silicone after exposure to 650°C reveals no significant microcracking.
A more detailed analysis by optical microscopy in lieu of the visual inspection can also be used. This allows more thorough inspection of microcracking and characterisation of crack width and crack length. Research has revealed one form of microcracking to be an oxidative mechanism with cracking initiating at the surface and progressing through the coating as it is exposed to longer periods of heat and oxygen exposure at the base of the crack.
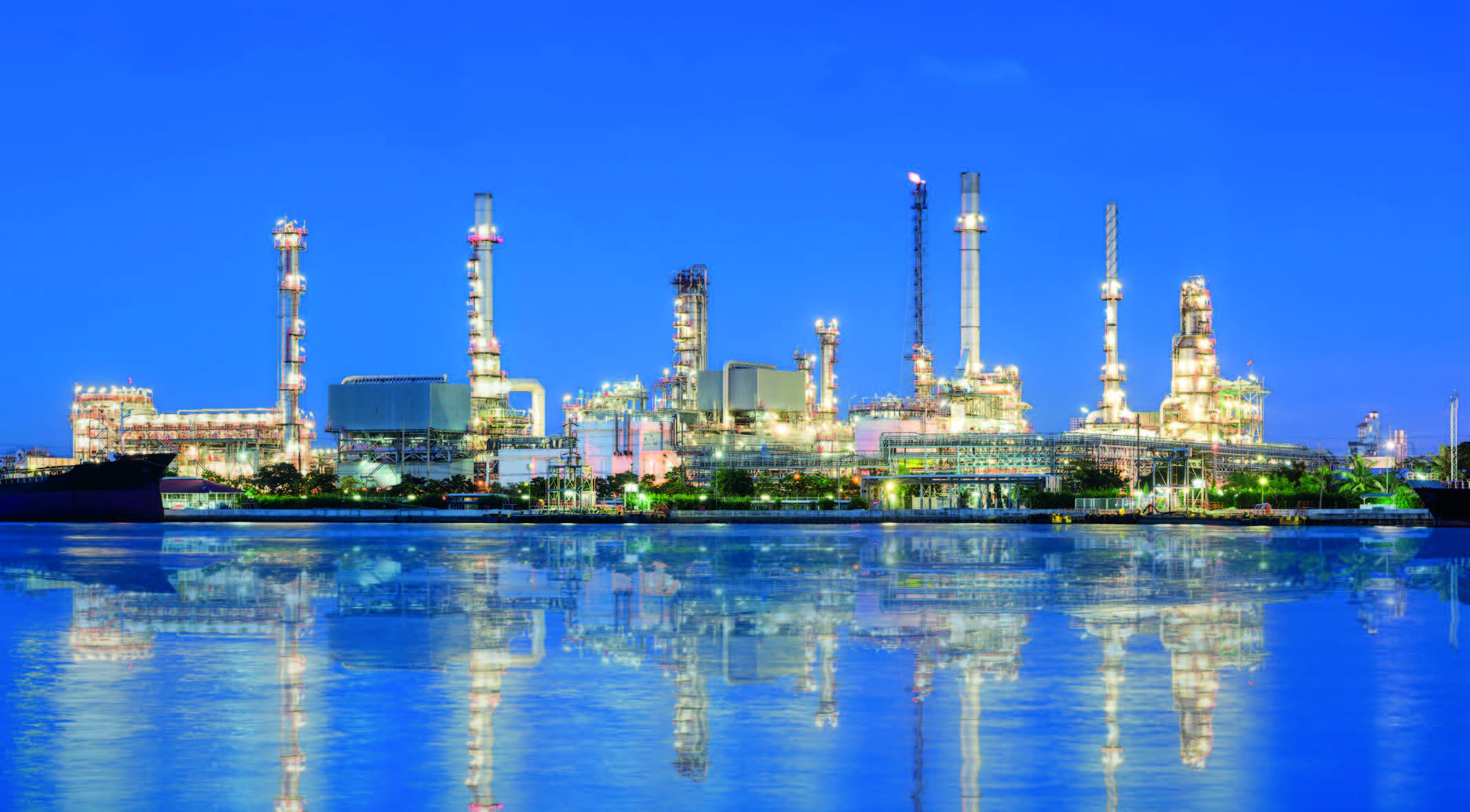
Modified versions of this test carried out at low temperatures can determine a coating’s ability to withstand cryogenic conditions.
ASTM D2402 describes the use of thermogravimetric analysis (or TGA). This uses highly accurate measurements of mass loss as a small sample of coating material is heated. This can be useful to characterise the polymer backbone in a coating material and the temperature at which degradation begins. Significant mass loss may also be indicative of porosity within the final coating film.
Other methods of thermal analysis such as Differential Scanning Calorimetry (DSC) can be used to highlight key events in the thermal profile of a coating. Events such as glass transition temperatures and the degradation onset temperature can all help to paint a picture of the coating material’s behaviour about heat exposure.
b) Simulating CUI conditions
Immersion test data is in many instances presented as being a worst case and thereby used as a standalone method for testing whether a coating can prevent CUI. While in some cases this may be true, it has some failings as a test method.
Firstly, it may actually discount some coating systems, which would work quite satisfactorily in real life. Additionally, it does not take into account the interaction between the insulation material and the coating itself. The passage of water through insulation may result in a change in composition of the corrosive medium, which is not automatically factored in into immersion testing. Test methods such as NACE TM0174 Method B can provide some information in this area; however, immersion testing is suggested to be supplemented with actual testing of insulated samples. Generally, the immersion testing is carried out at elevated temperature.
Many coating manufacturers have also developed an ad hoc cyclic test, which incorporates an element of immersion. Typically, this would involve the heating of a sample panel to a given temperature by means of an oven, immediately quenching it in cold water and then immersing the sample in boiling water. A typical cycle could be:
- overnight (16 hours) heating at 200ºC
- immediate immersion in cold water 5ºC, followed by
- 8 hours immersion into boiling water at 96ºC
While this test might include the additional internal stresses on a coating resulting from cyclic conditions, the arguments listed above under immersion testing would also be appropriate here.
Generally for both of the above tests, evaluation post exposure is carried out to ISO 4628 Parts 25, looking for blistering, rusting, cracking and flaking, respectively. Pre and post exposure adhesion evaluation is also common via test methods such as ASTM D4541 or ASTM 3359 in the case of softer silicon based materials.
ASTM G189 determines the corrosion rate and is isothermal. While initially designed for metallic materials, this test method can also be adopted for non-metallic materials. A pipe is filled with oil and a number of metallic ring specimens are placed over the pipe in thermal contact with the pipe and separated by electrically nonconductive spacers made from a suitably temperature resistant material. The assembly is then wrapped in insulation and sealed allowing an annular space to form where the corrosive fluid can collect. A corrosive fluid can be varied and can also be produced to simulate potential leachates from the insulation process. The corrosive fluid is then repeatedly pumped into the CUI cell at a controlled rate.
Based on this, various temperatures and wet dry cycles can then be applied to the CUI cell. At the end of the test programme, mass loss measurements are taken and a corrosion rate is determined. Electrical measurements, such as EIS can also be carried out.
It is worth emphasising that the ASTM G189 test is essentially isothermal. A constant test temperature is maintained (within a predetermined range). This is unlike the cyclic insulated pipe test, or the so-called Houston pipe test, where the temperature at any given point varies along the length of the pipe and the level of saturation of the insulation, which is dependent upon the duration of exposure.
A number of operators have carried out testing which involves taking the basic principle of ASTM G189 and scaling it up to larger test programs. Instead of a single pipe, a number of small diameter pipe spools are coated and bolted together. Each pipe spool is electrically isolated from the next. The pipe is then insulated. A heated medium (either air or oil) is then passed through the pipe, heating the substrate and a corrosive medium is passed into the insulation. This test can be carried out using a pump type arrangement or by lowering the whole assembly into a water trough and raising the level of the corrosive medium up and down on a cycle to saturate the insulation and then allow it to dry out.
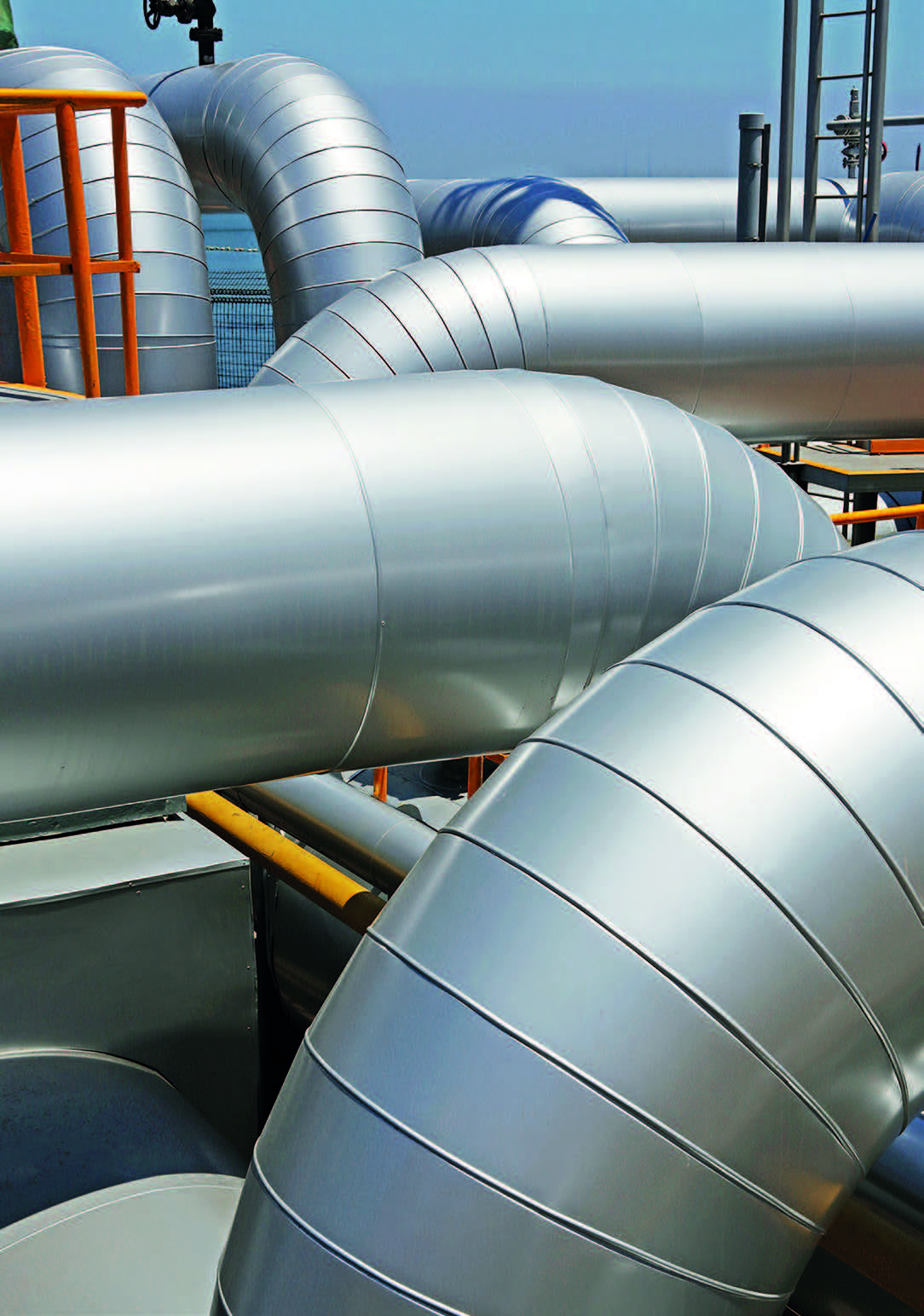
One of the main benefits of this test method is that the larger surface area allows better evaluation of the chosen coating system post exposure. Electrical measurements can be undertaken.
Though costly and requiring a significant amount of space, this method also allows variables such as test temperature, wet dry cycle duration, type of insulation, and insulation standoff to be evaluated in a more representative manner.
The Cyclic insulated pipe test (the Houston pipe test) was designed to rapidly determine information about a coating’s performance at different temperatures in a single test. A coated piece of pipe (typically 50 mm in diameter) is stood vertically on a hot plate. The temperature is set to achieve the desired test temperature range over the length of the pipe. The pipe is insulated with the chosen insulation type, e.g. mineral wool or calcium silicate. The insulation is saturated with a salt solution before raising the hotplate temperature. The temperature is then maintained for a period of time, typically 8 hours and additional salt solution is added prior to cooling.
The principle drawback with this test method is that 1) the temperature profile of the pipe changes with the type of insulation used and 2) as the level of saturation of the insulation increases over the duration of the test, it lowers the test temperature.
In principal, it is exceptionally difficult to correlate the thermal exposure that a particular point on the pipe has been exposed to. This is important particularly for those materials where the property of the coating changes with thermal exposure.
As such, it is useful to ensure that test samples, which have been thermally conditioned prior to exposure, are also included in any test program.
The CUI test chamber consists of a square steel section 4”x4” 24 inches long with a ¼ inch wall thickness, which is placed horizontally in the test chamber. Hot oil from a heat exchanger is circulated through the cell and the temperature is controlled from ambient to 250ºC. The bottom portion of the cell is under continuous immersion for the duration of the wet cycle. Various cycles can then be programmed. An intentional defect or scribe is routinely added to evaluate for corrosion creep, and similar post exposure measurements such as mentioned in some of the previous tests can also be carried out.
One of the major drawbacks of this type of arrangement, however, is that the absence of insulation prevents you from evaluating the effect of insulation type.
c) Tests not necessarily directly related to CUI
When considering protective coatings for insulated pipework and process equipment, the following tests might be useful.
Salt spray testing has been largely superseded by cyclic corrosion test methods. It is, however, still widely used by coating manufacturers and in some international standards such as ISO 12944: 1998 Part 6 .
The salt spray test consists of exposing panels to a corrosive solution for a given duration and measuring for the presence of rusting, blistering, flaking, disbandment and rust creep from an intentional scribe. Different standards utilise different key variables, such as electrolyte make up, temperature and test duration. While this type of test procedure may be useful in comparing and ranking materials, it offers limited correlation to actual exposure.
Cyclic corrosion testing, such as prescribed in ISO 20340: 2009 or ASTM D5894 : 2010 combines an anticorrosive test such as salt spray in conjunction with other exposures such as UVA, condensation and low temperature cyclic to produce a test more representative of actual atmospheric exposure.
While accelerated corrosion methods are a necessary part of coating development and qualification, actual atmospheric exposure at a site, which has been measured as able to provide a specific level of corrosion, remains the most reliable means of determining a coating’s ability to withstand atmospheric corrosion although of course longer exposure periods are required.
Measurement of coatings physical properties such as hardness, impact resistance and abrasion resistance may provide some guidance on a material’s physical durability. Corrosion resistance is of course a primary requirement; however, the presence of undetected mechanical damage arising from the construction process can undo much of the good work done by specifying and selecting the correct type of protective coating. This is increasingly important given the high levels of prefabrication found on modern day construction projects.
Often coatings used in insulated and uninsulated conditions may go some time before being overcoated to provide the necessary aesthetic appearance or for safety reasons in the case of pipe markings. In many cases, this could take place in an entirely different location. Measurement of a coating material’s ability to be overcoated after extended periods can easily be verified using a physical adhesion method such as ASTM D4541 although some form of exposure testing is preferred for truly conclusive results.
New ISO standard
In 2018 a new ISO standard was introduced ISO 19277:2018 Petroleum, petrochemical and natural gas industries - qualification testing and acceptance criteria for protective coating systems under insulation.
This standard contains many of the elements described above and was designed to provide guidance when pre-qualifying coatings for use in preventing Corrosion under Insulation (CUI).
3. Conclusions and advice
When choosing the right coating for a specific purpose in a specific environment it is crucial to look at which tests the coating has undergone.
The CUI coating Versiline CUI 56990 has been tested and proved to be able to provide long-term protection for how pipework, equipment and other hot surfaces. Tests also show that it is very resistant to micro-cracking, even in an environment with extreme temperatures. Versiline’s barrier pigments make it highly effective against CUI, even under cyclic conditions.
The described processes within this paper should have provided some insight into the complexity of the testing required to determine a protective coating’s ability to prevent or delay the effects of corrosion under insulation.
Some key points to take away include:
- Select a test method, which allows you to determine the coatings resistance to heat / temperature, not just using the operating temperature as a guide but other likely conditions that the coating will encounter (upsets, thermal cycling etc.)
- Once this has been determined, identify a suitable test for corrosion under insulation and use this to determine the coating’s resistance. Consider the effects that any prior thermal exposure may have on the coating’s behaviour
- Where a coating has been selected for a dual use including atmospheric exposure, ensure that this has also been thoroughly evaluated, don’t simply rely on the corrosion under insulation test results
- Use protective coatings carefully as part of an overall CUI methodology, which includes optimal design, best installation practises and current inspection and detection techniques to prevent corrosion under insulation really hurting you
-
Notes
- By the Danish Technical Universit
- Salt spray test methods such as ISO 7253 (Neutral salt spray) and ASTM B117 (standard practise for operating Salt Spray (Fog) apparatus) can be consulted for further guidance