Summary
Intumescent coating systems are one of a range of available passive fire protection (PFP) systems designed to contain and minimise the effects of a fire. Intumescent coating systems have a number of advantages over other PFP systems. They are easier to apply and maintain than concrete casings or fire-resistant boards, for example, and can be overcoated with any decorative or protective finish. As a result, intumescent coating systems are increasingly specified both on new constructions and renovations of existing buildings.
Intumescent coating systems have improved durability when used with primers and/or topcoats, which is important in demanding exposure conditions. However, it is essential that all coatings in the system are compatible and approved in order to ensure fire protection performance. If the primer and/or topcoat is not compatible, the system may require maintenance or reapplication earlier than specified, resulting in added costs for the building owner. In the worst case, the primer or topcoat may have an unintended negative effect to the intumescent coating’s fire protection properties.
What are intumescent coatings?
When steel is heated above 500ºC, it quickly loses half of its room temperature strength. In a fire, unprotected structural steel can reach this stage in less than 15 minutes – and the structure can collapse as a result.
Intumescent coatings are reactive coatings that enable structural steel to maintain its load-bearing capacity during a fire for a specified duration – known as the ‘fire duration’. When exposed to temperatures above 250ºC, the intumescent coating swells to form a layer of inorganic and carbonaceous char, which insulates the substrate from the heat of the fire. This enables the steel to maintain its load-bearing capacity for longer. As a result, there is more time for evacuation of the building and emergency response, and firefighters have more time to put out the fire.
Slip test procedure
When used for fire protection of steel in demanding exposure conditions, intumescent coating systems usually comprise several layers of different paints, typically a two-coat system (primer + intumescent) or three-coat system (primer + intumescent + topcoat). The choice of system depends on the potential corrosivity/weathering of the external environment.
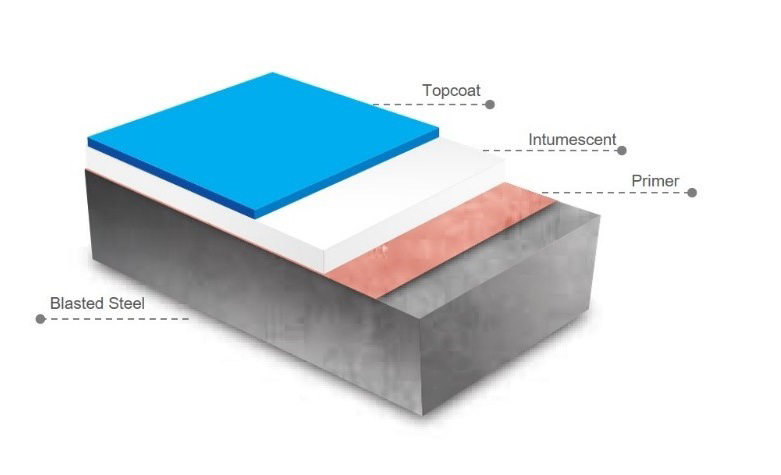
Figure 1. A typical intumescent coating system
Each of these coats plays in important role in the coating system. Therefore, it is essential that all coats in the coating system have been tested together. During official fire testing of intumescent products at third-party laboratories, each intumescent product is tested on top of one type of primer (in some cases, also with a topcoat) at a specified dry film thickness. The use of other primers and topcoats from the same paint manufacturer with that particular intumescent product is possible following further testing.
For this reason, paint manufacturers approve specific primers and topcoats as part of their intumescent coating systems, using recognised industry standards, including the most widely used EOTA’s European Assessment Document EAD 350402-00-1106 and the CEN’s European Standard EN16623. In some cases, manufacturers may decide to do more testing than is strictly mandatory to check other important properties, such as adhesion in cold-state or recoating intervals.
The role of the primer coat
In a standard coating system, the primer ensures adhesion to the substrate as well as additional anti-corrosion protection to the steel. When used as part of an intumescent coating system, the primer has an additional function: to ensure adhesion of the carbon char to the steel during a fire. This is known as ‘stickability’.
The majority of primers used in intumescent systems are standard anti-corrosive primers, with no inherent heat resistance properties. It is common for primers to lose adhesion to the steel substrate when exposed to high heat, especially when applied in high dry film thicknesses. During a fire, this may result in a detachment of the intumescent char layer, exposing the steel to a rapid temperature rise and potentially compromising the intumescent coating. Therefore, the primer needs to be tested and approved as part of the intumescent system.
Testing and approving primer families
According to EAD 350402-00-1106, primers are tested and can be approved on a generic basis (i.e. if one primer type is demonstrated to work at a specified dry film thickness, the whole generic primer family can be approved). As indicated above, the dry film thickness of the primer is a key factor. For this reason, each primer family is specified to a maximum dry film thickness (not exceeding 200 microns). The final approval of a primer should always be provided by the manufacturer of the intumescent coating.
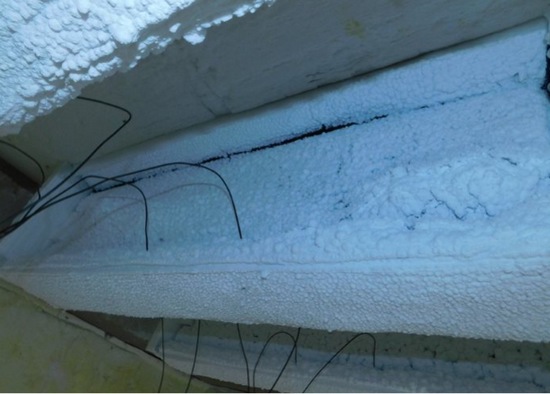
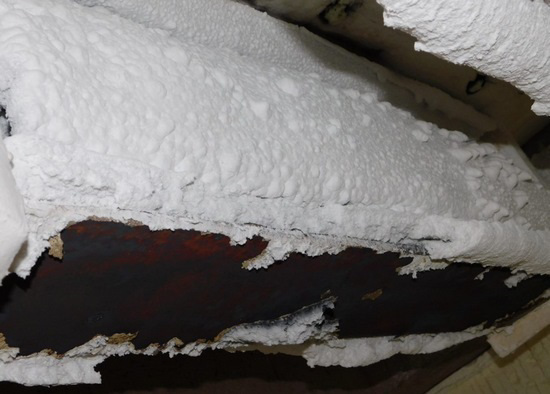
Figure 2. The importance of ‘stickability’ in primers: The image on the left shows char that is well formed and adhered to the substrate; the image on the right shows where poor stickability has exposed the steel to fire.
The role of the topcoat
The topcoat provides the coated surface with an aesthetic and colour. However, in more demanding exposure conditions, for example above C3, its most important function is to provide a seal coat for the intumescent layer. This ensures the intumescent coating is not attacked by moisture or other environmental factors. Therefore, the choice of topcoat is dependent on the weathering and corrosive conditions the coating system will be exposed to.
The sealing effect is dependent on the type of topcoat (normally based on the binder chemistry) and the applied dry film thickness. The use of an incompatible topcoat or dry film thickness that is too low will result in a lack of protection for the intumescent coating. This will lead to early degradation of the intumescent coating and the eventual loss of its char-forming properties. If the dry film thickness is too high, the topcoat may impede char formation, resulting in a shorter fire duration.
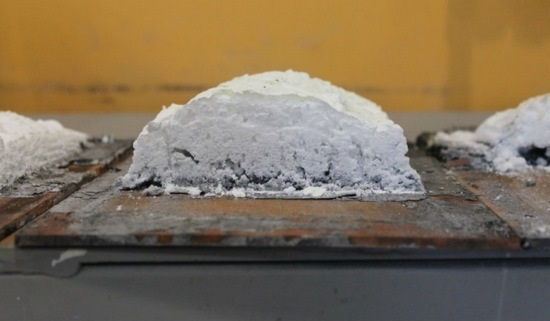
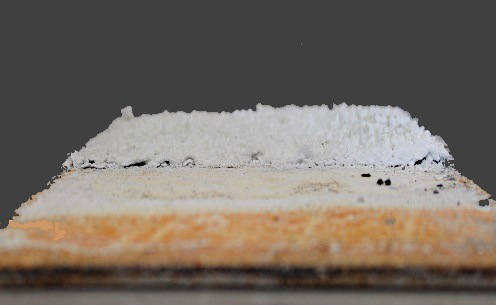
Figure 3: The importance of the sealing effect: The image on the left shows good char expansion; the image on the right is of an exposed and degraded intumescent, which shows no char-forming properties.