Context
The IMO sulphur cap becomes effective on 1 January 2020. This requires all vessels to limit their sulphur emissions to 0.5 per cent from the current limit of 3.5 per cent.
In order to comply with the new, reduced limit shipowners, have three main options:
- Burn low sulphur bunker fuel oil (LSFO) instead of the current high sulphur fuel oil (HSFO).
- Continue to burn HSFO and install a scrubber in the vessel’s funnel to remove the sulphur before the exhaust is released into the atmosphere.
- Switch from engines that burn traditional fuel oil to engines that burn LNG instead. LNG exhaust contains almost zero sulphur content.
Discussing the options
LNG engines are really only suitable for newbuild vessels. Whilst it is technically possible to retrofit, the economics don’t add up for most owners. This is not really a viable option for most existing ships and therefore is not considered further in this paper.
Burning LSFO is perfectly feasible but the difference in price between LSFO and HSFO is likely to be significant and will vary depending on prevailing market forces.
The supply and availability of sufficient quantities of LSFO is also in doubt. However, burning LSFO requires very little upfront investment and/or change to the vessel’s machinery. This is likely to be the preferred option for most shipowners, at least in the early years.
Installing a scrubber is an expensive option as the equipment is likely to cost between USD 2 to 8 million per vessel. Installation requires dry docking the ship which will take it out of service (and therefore off-hire) for 2-3 weeks. Currently, there is a shortage of scrubbers and dry dock availability.
However, once installed, the vessel can continue to burn the less expensive HSFO and the savings made will, in time, pay for the upfront investment made. Clearly, the age of the vessel must be taken into account (there is little point in installing a scrubber in an elderly vessel) as well as the future price differential between LSFO and HSFO.
[Note: Scrubbers use either open or closed loop technology. In an open loop system, the sea water used to clean the exhaust (known as wash water) is discharged directly back into the sea. A closed loop system reuses the wash water and stores it onboard for later discharge in port. Some ports and maritime authorities are already banning the use of open loop scrubbers in their urisdictions because of a potential pollution risk. This is having a further impact on the choice of compliance option.]
The importance of the price of LSFO
It is not possible to know what the actual price of LSFO will be on 1 January 2020, or beyond. Commentators have given estimates of between USD 100 to 300 per tonne more than HSFO.
The price differential is important as potential savings (ie the savings realised by installing a scrubber and burning HSFO as opposed to burning LSFO) can be used to offset the scrubber installation cost. If the gap between the price of LSFO and HSFO is wide, the payback period relating to the cost of installing the scrubber is relatively short. As the price gap narrows, the payback period lengthens.
Example
To illustrate the importance of the price differential, we assume it costs USD 6 million to fit a scrubber to a VLCC. The lifespan of the scrubber is 15 years. In the table below we run four scenarios where the price of LSFO and HSFO (and the difference between them) differs.
When the price differential is 20 per cent (scenario 1) and the price of HSFO is relatively high, the scrubber payback period is just 3.3 years. If the price of HSFO drops, but the differential remains the same (20 per cent), the payback is pushed out to 4.2 years. If the price differential grows to 50 per cent, the payback reduces to 1.3 years (scenario 3); and if there is no price difference between HSFO and LSFO, then there is no price advantage and therefore zero payback (scenario 4).
According to Clarksons Research, only around 3.000 ships (from a potential 60.000) will be fitted with scrubbers by the 2020 deadline.
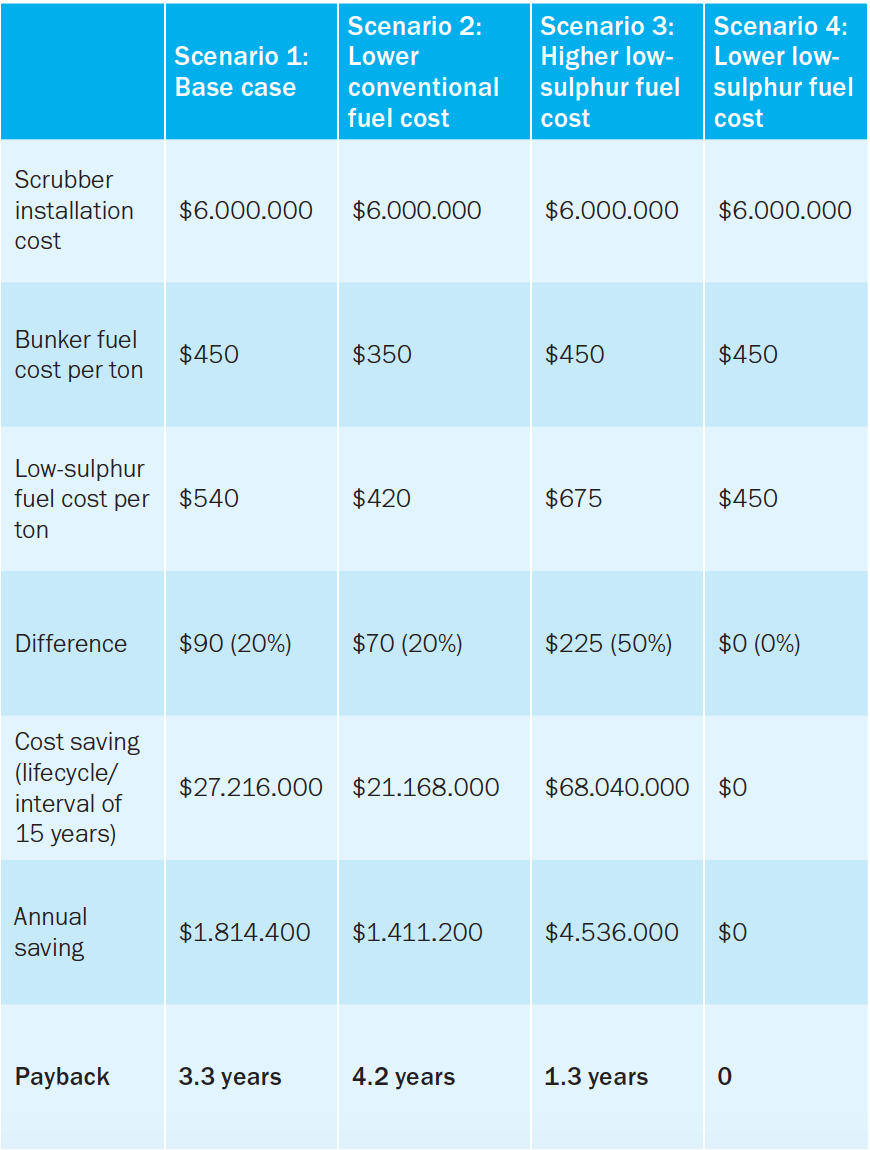
In these calculations, the daily fuel consumption of the vessel is assumed to be 80 tons, with an annual activity level of 70 per cent.
How does the optimum choice of coating make an impact?
A good hull coating will minimise speed loss
Speed loss is the difference in speed achieved by a vessel with a clean hull as compared with the same vessel with a fouled hull when the engine power output is identical.
Taking a VLCC as an example, if the shipowner had chosen a market average hull coating, the average speed loss over a five-year period would be around 18 per cent. Selecting a premium coating (such as Hempel’s Globic 9500 or Hempaguard X7) the speed loss can be significantly reduced to just 1.4 per cent over the same five year period. This corresponds to the same shipowner achieving a 13.5 per cent fuel saving over five years.
Using an optimum hull coating will improve efficiency when burning either HSFO and LSFO and improve payback periods further and/or offset the cost of the more expensive LSFO.
In the table below we consider the scrubber/HSFO option together with a premium hull coating. The savings generated from this option allows the owner to payback his investment in the scrubber and coating in just over 5 years. If the owner had opted for the market-average coating, no fuel savings would have been made and so the cost of the scrubber (and the coating) would not have been recovered.
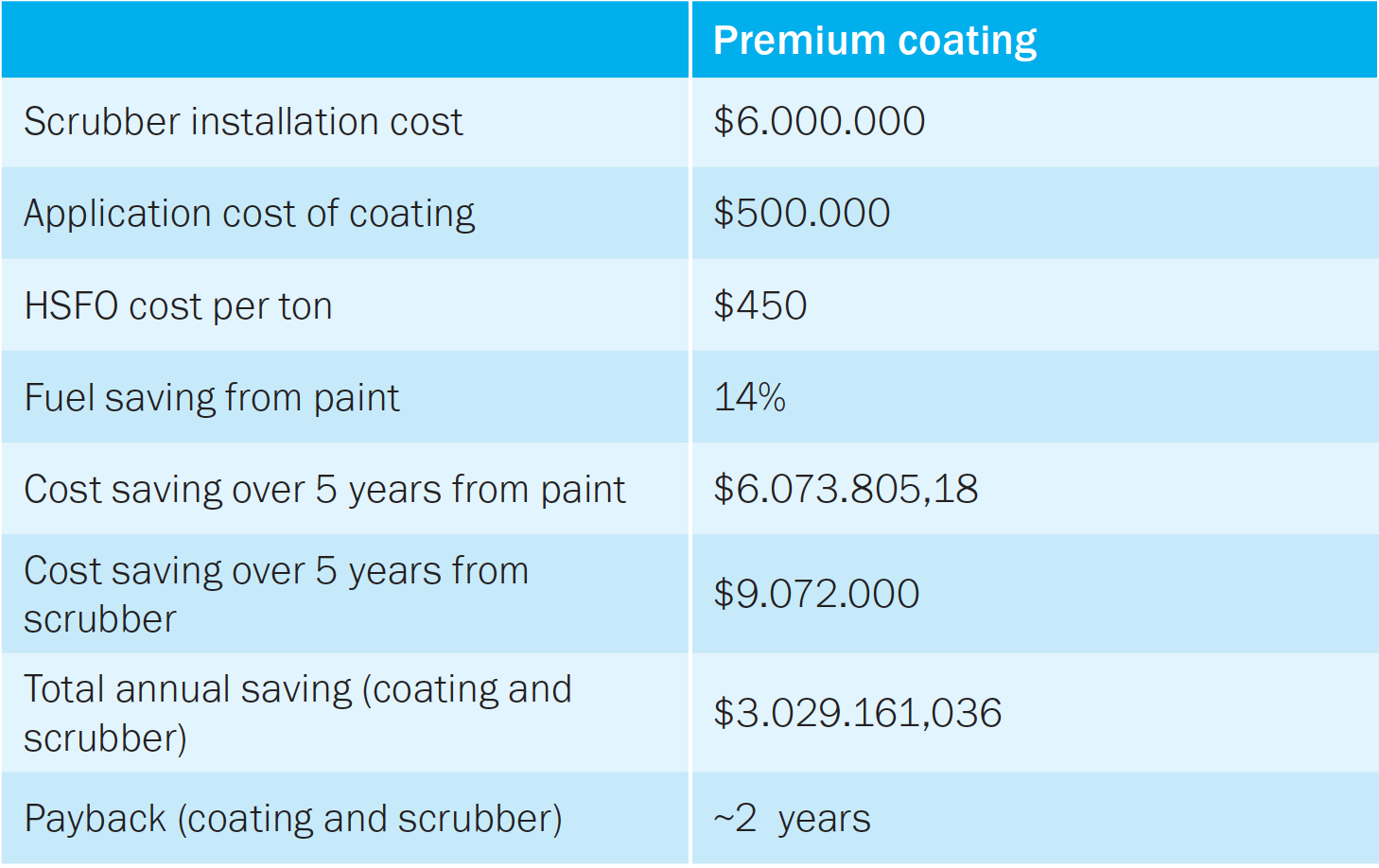
In these calculations, the daily fuel consumption of the vessel is assumed to be 80 tons, with an annual activity level of 70 per cent.
The next table considers the more expensive LSFO option. Using a premium coating delivers payback on the costs of the coating in just under four months and annual savings of more than $1.4 million.
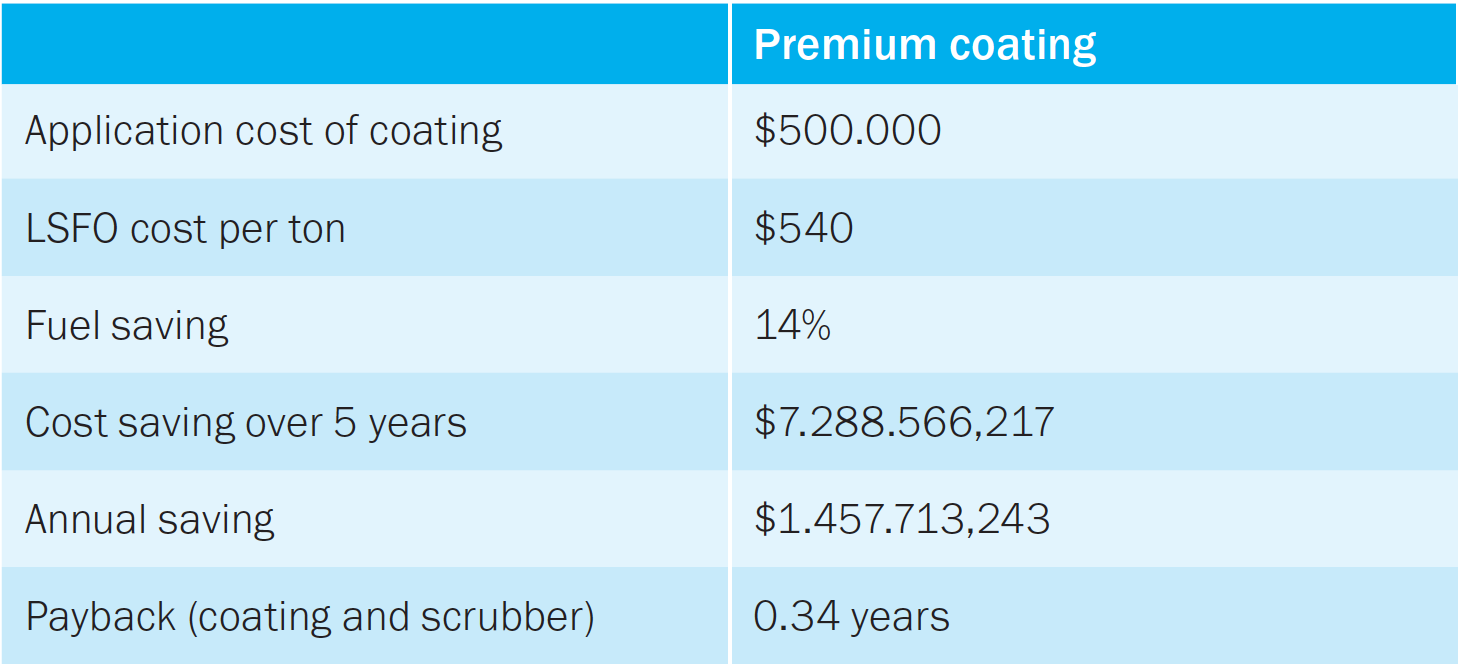
In these calculations, the daily fuel consumption of the vessel is assumed to be 80 tons, with an annual activity level of 70 per cent.
Conclusion
Shipowners have a clear decision to make between opting to install a scrubber and continuing to burn HSFO, or switching to the low sulphur alternative.
Whilst Hempel cannot advise which option to select, it can demonstrate that by applying a premium hull coating, the shipowner is able to offset the associated costs.
The savings generated from using a premium hull coating will “payback” the cost of a scrubber and the coating within a 5 year time-frame (using the example above). Whereas the application of a market-average coating will not achieve any savings and, therefore, not contribute to the scrubber/ coating costs.
If the owner has opted to burn LSFO, the savings achieved by using a premium hull coating will “payback” the cost of the coating within a few months and deliver around $1.5 million a year to help offset the cost of the more expensive LSFO.
It is clear that choosing a high performance hull coating delivers significant cost benefits over a market-average alternative irrespective of which sulphur compliance option is selected.