Striking the perfect specification balance for one of the world’s largest desert water parks
A major water park project, located in Saudi Arabia, is a groundbreaking initiative aimed at creating one of the world’s largest water parks with an area of 252,000 m2.
In 2022, our client was appointed as the lead design consultant tasked with not only designing the park but also supervising its construction.
The project’s size and scope called for advanced knowledge in corrosion and passive fire protection – expertise that led to Hempel’s involvement.
In 2022, our client was appointed as the lead design consultant tasked with not only designing the park but also supervising its construction.
The project’s size and scope called for advanced knowledge in corrosion and passive fire protection – expertise that led to Hempel’s involvement.
The challenge
Ensuring steel protection across diverse exposure conditions
The specification challenges faced in this water park project were both unique and multifaceted.
The primary concern was the direct exposure of steel structures to Saudi Arabia’s arid climate coupled with the unique challenges of a water park’s microclimate — hot and humid conditions with limited chloride and sulphate content. This setting demanded a careful selection of coatings that could withstand such conditions without compromising the integrity of the steel.
The primary concern was the direct exposure of steel structures to Saudi Arabia’s arid climate coupled with the unique challenges of a water park’s microclimate — hot and humid conditions with limited chloride and sulphate content. This setting demanded a careful selection of coatings that could withstand such conditions without compromising the integrity of the steel.
Furthermore, in specification processes where uncertainty is high, there’s often a default approach to over-specify as a precautionary measure for ensuring safety and protection. However, this could lead to significantly higher costs without additional benefits — a significant consideration for a project budgeted at $750 million.
Recognising the delicate balance required for a project of this size, the consulting engineers turned to Hempel’s specialised coating expertise for precise and clear specification guidance.
Recognising the delicate balance required for a project of this size, the consulting engineers turned to Hempel’s specialised coating expertise for precise and clear specification guidance.
The solution
Assessing the exposure conditions for custom specifications
Hempel initiated an assessment process to tailor-make coating specifications suited for the demanding C4 corrosivity environment of certain areas of Saudi Arabia and the microclimate within the park. The process of developing these specifications was rigorous and detail-oriented, focusing on the park’s unique conditions.
Hempel assessed diverse exposure conditions in the park, from direct environmental exposure to concealed steelwork, necessitating varied protection levels. This entailed detailed specifications for each exposure category, specifying coatings, application methods, and expected results.
Hempel assessed diverse exposure conditions in the park, from direct environmental exposure to concealed steelwork, necessitating varied protection levels. This entailed detailed specifications for each exposure category, specifying coatings, application methods, and expected results.
For instance, for external elements directly exposed to the environment and requiring intumescent fireproofing, Hempel specified a threelayer system starting with an activated zinc epoxy primer, followed by a solvent-based, acrylic, physically drying intumescent coating, and completed with a high solids acrylic polyurethane topcoat. This system was designed to offer both fire protection and aesthetic appeal, with colour and gloss retention over time.
Hempel’s specifications were highly regarded, prompting the consulting engineers to directly incorporate them into their project requirements.
Hempel’s specifications were highly regarded, prompting the consulting engineers to directly incorporate them into their project requirements.
Key takeaways
The learnings from the water park project should inspire future projects to prioritise detailed, environment-specific planning and innovation within their specifications.
-
1. Understanding corrosivity categoriesRecognising the correct corrosivity category is crucial for developing durable coating systems that withstand environmental challenges without over-specification. This ensures that solutions are not only compliant but also perfectly tailored to the project’s needs.
-
2. Customisation is keyThe project emphasised the importance of custom solutions, particularly in coating specifications. Engineers and specifiers are encouraged to seek solutions tailored to the unique conditions of their projects to avoid under- or over-specification.
-
3. Collaboration for successThe project highlighted the essential role of teamwork among engineers, coating advisors and specialists. Open dialogue and
detailed technical discussions help clarify specifications and adapt to evolving project needs, ensuring successful application and collaboration.
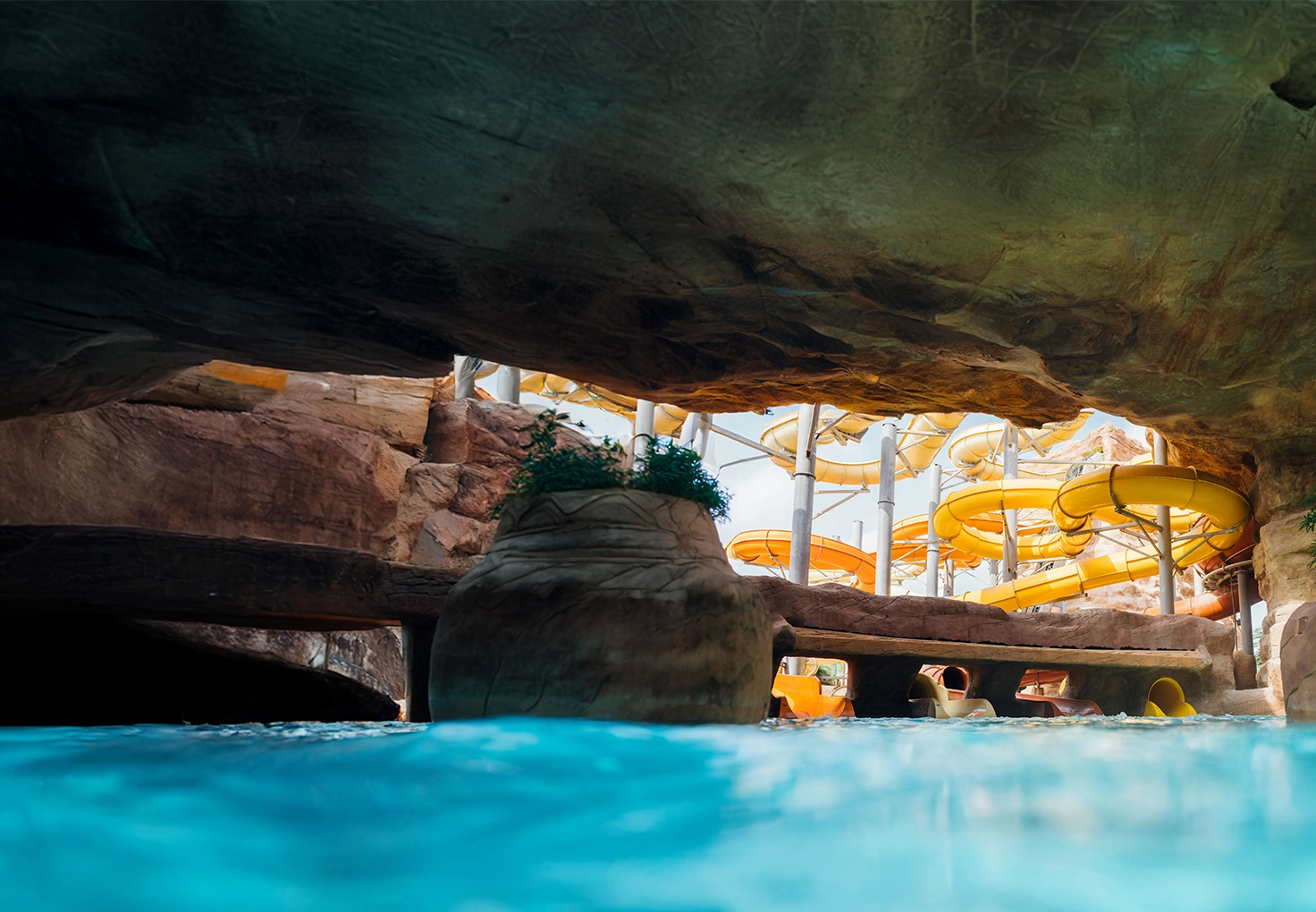
The coating system
Hempadur Avantguard® 550 is an activated zinc epoxy primer that reduces corrosion and provides excellent galvanic protection. It dries quickly, offers outstanding mechanical strength, and has superior tolerance to high relative humidity during application.
For externally exposed steel, Hempafire Pro 400 offers up to 120 minutes of passive fire protection against cellulosic fires. It is a one-component, solvent-borne, intumescent coating that has been rigorously tested and approved. For selected areas, Hempafire Optima 500 provides passive fire protection with a very low VOC, one-component water-borne intumescent coating, specifically designed for structural steel against cellulosic fires.
For externally exposed steel, Hempafire Pro 400 offers up to 120 minutes of passive fire protection against cellulosic fires. It is a one-component, solvent-borne, intumescent coating that has been rigorously tested and approved. For selected areas, Hempafire Optima 500 provides passive fire protection with a very low VOC, one-component water-borne intumescent coating, specifically designed for structural steel against cellulosic fires.
Local Hempel advisor:
Reem Abdo,
Business Development Manager,
Hempel Paints (Emirates) LLC.
Reem Abdo,
Business Development Manager,
Hempel Paints (Emirates) LLC.
Hempathane HS 55610 is a high-solids acrylic polyurethane topcoat known for its excellent gloss and colour retention. It is specifically designed to protect structural steel in severely corrosive atmospheric environments.
This coating system was specified to offer both fire protection and aesthetic appeal, with excellent colour and gloss retention over time.
This coating system was specified to offer both fire protection and aesthetic appeal, with excellent colour and gloss retention over time.